3 Types of CNC Spindles and How to Choose the Right One
When it comes to machine tools, the spindle plays a crucial role, especially in metal cutting machines. The selection of the right spindle is essential for achieving optimal performance and efficiency in machining operations. In this post, we'll explore the three broad categories of CNC spindles and discuss the factors to consider when choosing the appropriate spindle type. This information is valuable for professionals in the manufacturing industry, particularly those involved in metal machining processes.
Selecting the right spindle for a specific application is vital for several reasons. It directly impacts the quality of the machined components, overall productivity, and operational costs. By understanding the different spindle types and their capabilities, manufacturers can make informed decisions to optimize their machining processes, ensure better surface finishes, reduce noise levels, and improve overall efficiency.
Belt Driven Spindles:
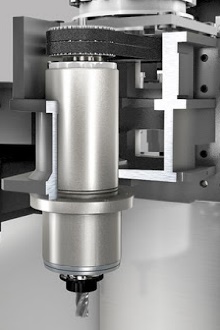
Belt driven spindles are popular for their versatility, allowing for easy adjustment of pulley ratios or the addition of gearboxes to achieve higher torque. They are suitable for speeds up to 8000 rpm, making them a reliable choice for a wide range of applications. However, beyond this speed, noise levels and the risk of belt slippage increase, potentially causing damage to the workpiece, tooling, and spindle itself.
Direct Driven Spindles:
Direct driven spindles eliminate slip between the motor and spindle, resulting in improved surface finishes, reduced noise, and easier maintenance. They are typically used for lighter materials like aluminium and copper and can operate at speeds up to 12000 rpm with minimal issues. However, direct driven spindles have limitations in torque multiplication, and if higher torque is required, motor capacity may need to be increased.
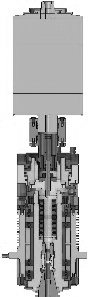
Integrated Spindles:
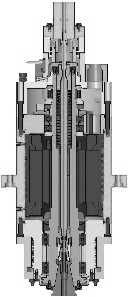
Integrated spindles, also known as built-in motor spindles, are an excellent choice for applications requiring high speeds and precision. These spindles have the motor and rotor integrated, offering enhanced accuracy and reduced noise levels. They are commonly used in industries such as aerospace, space components, and electronics, where close tolerances and high-speed requirements are critical. Integrated spindles often feature ceramic bearings, further reducing noise and minimizing heat generation.
Choosing the right CNC spindle is crucial for achieving optimal machining results. Belt driven spindles offer versatility, direct driven spindles provide improved surface finishes, and integrated spindles excel in high-speed and high-precision applications. Manufacturers must consider factors such as speed requirements, torque demands, material characteristics, and accuracy needs when selecting the appropriate spindle type. By making informed decisions, businesses can enhance productivity, quality, and overall efficiency in their metal cutting processes.
Ready to optimize your machining processes? Contact us today to discuss your specific requirements and find the perfect CNC spindle for your application. Improve your productivity and achieve superior machining results with the right spindle choice.